Manufacturing innovative composites materials for a cleaner planet
The CEM-WAVE project plans to create new, more resistant, and sustainable materials for steelmaking and heavy industry manufacturing. How can oxide-based ceramic matrix materials play a role in the ecological transition?
By Zhongmin Li (University of Birmingham, UoB)
In 2018, the European Commission set the strategy “A Clean Planet for All”, a long-term vision for a European climate neutral economy. Then, in 2019, the European Green Deal was published, with new ambitious priorities aimed at Europe becoming the first climate-neutral continent by 2050.
A considerable R&D effort is ongoing towards reaching this objective and the CEM-WAVE project is an example. CEM-WAVE focuses on improving energy efficiency by developing new, high-performance materials that can withstand the typical demanding conditions of energy generation and energy-intensive industries, such as steelmaking.
The CEM-WAVE project, which started in October 2020 and will last four years, is focused on materials known as ceramic matrix composites, or CMCs. Although these have existed for a few decades, their high production costs restricted their widespread application in the high energy process industry. Thus, a major goal of the programme is to develop an innovative lower-cost manufacturing process; this is Microwave-assisted Chemical Vapour Infiltration (MW-CVI).
Whilst not yet commercialised, this novel process has the potential to significantly shorten the time needed to make components, potentially by an order of magnitude, hence significantly reducing the costs for making CMCs components.
The work at the University of Birmingham concentrates on manufacturing oxide-based CMCs. These are materials that do not have the same high-temperature capabilities as the more commonly used non-oxide versions but are considerably less expensive. Oxide-based CMCs have rarely been made before by the MW-CVI technique, so this is completely new research.
The main issue is that oxide ceramics generally do not absorb microwaves, but we believe that we can successfully overcome this by applying coatings. We hypothesise that the coating would have a dual function, allowing microwave absorption and helping to improve the toughness of the materials by appropriately modifying the interfaces between the composites’ reinforcement fibres and their matrix. Therefore, we can categorise this research as posing quite a high risk but with the potential for very high gains - should it work.
A key advantage of microwave heating is the volumetric nature of the energy absorption in those materials that absorb microwaves. In contrast to conventional furnaces, where we generate heat by conduction or radiation, microwave energy is directly absorbed by the material and is proportional to its volume. Consequently, the heating rate can be much higher. In MW-CVI an even more important feature is that an “inverse temperature profile” develops due to the material being heated directly, with some heat loss at its surface.
This practically means that the centre of the material is hotter compared to its surface, allowing the heating process to happen from the inside towards the outer layers. For SiC-based composites, MW-CVI reduces the processing time from roughly 1000 hours spread across multiple infiltration runs to a single run of around 100 hours. The significant reduction in processing time should result in cheaper materials.
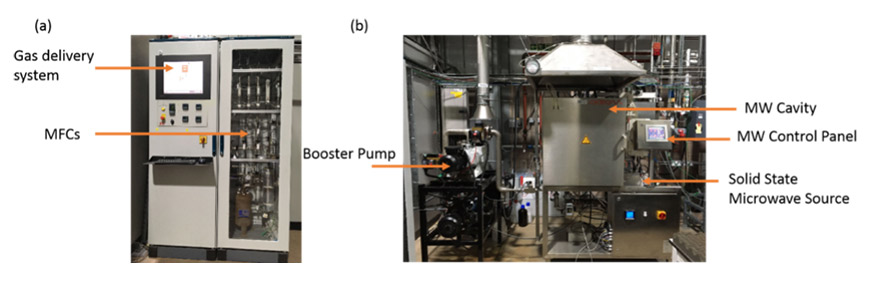
Previously, MW-CVI has been successfully used to produce SiC/SiC composites. UoB built a CVI system around a decade ago, to conduct scientific studies on the subject. You can see it in Figure 1 below. However, the manufacturing of CMCs based on alumina fibres and an alumina matrix is much more challenging since alumina is more or less transparent to microwaves – especially at low temperatures.
Therefore, the existing MW-CVI system has been redesigned and is being upgraded to ensure that we can produce both the original SiC-based and the new alumina-based CMCs. The CEM-WAVE consortium member in charge of completing this work is Archer Technicoat Ltd (ATL) of High Wycombe, UK. Amongst other design features, we fitted a solid-state microwave source. This will provide much greater control over the microwave power and frequency than the original magnetron.
This still leaves the question of how to “persuade” largely microwave-transparent alumina fibres and matrix to absorb microwaves. To address this, our team produced different types of coatings using either a dip-coating process here at UoB or a continuous roll-to-roll process at the Fraunhofer-Centre for High-Temperature Materials and Design in Bayreuth, Germany.
These coatings are designed to have a dual function. First, we adjust the dielectric properties of the initial alumina fibre preform so that it absorbs microwaves and can be heated. If we can get it right, the coatings should also improve the fracture toughness of the resulting composites by controlling what happens to cracks when they intersect the many fibre/matrix interfaces. Work is ongoing to look at different chemical precursors for the coatings.
Currently, we are investigating the dielectric properties of the coated fibre preforms as a function of temperature. In parallel, we are studying their microwave heating behaviour, both numerically, via multi-physics simulations of the reactor loaded with the sample, and experimentally by collaborating with another partner, the Institute for Chemical and Physical Processes at the University of Pisa in Italy.
The manufacturing of these alumina-based composites by MW-CVI looks promising but challenging. We are sure exciting results await us. If you want to know more about this exciting project and what we have in store, keep an eye on our news!