Modelling Chemical Vapor Infiltration with Microwave Heating: a multi-scale, multi-physics challenge
Understanding how CVI works under microwave heating is, to say the least, a complex business. Image-based modelling offers a chance to understand the complex interplay of physicochemical phenomena before setting them to practice
By Prof. Gerard L. Vignoles (Director of the Lab. For ThermoStructural Composites, CRNS)
As you had the chance to read in our preceding blog entry, Chemical Vapor Infiltration (CVI) assisted by Microwave (MW) heating is a specific variation of the basic CVI process involving the use of MW to obtain an inverse thermal gradient: cool outside and hot inside. The idea is to turn on the chemical deposition reaction leading to the infiltration of the ceramic matrix in the fibrous reinforcement of the composite only in the deepest parts of the material. The infiltration then progresses from the interior toward the external portions of the medium. In simpler terms, what we want to avoid is having a crust with a hollow crumb!
For the desired effect to display, it is necessary to have a correct idea of the interplay of physicochemical phenomena at several scales (i.e. a fibre scale, a tow-scale and a part-scale). And they are numerous! To begin with, we can simulate microwave heating by solving the Maxwell equations of electromagnetics (fortunately, without having to consider magnetism – phew!). Once this is cleared, we look at the spatial distribution of the heat sources in the material. Logically, the next step is then to solve a heat transfer equation, including the mentioned heat sources, plus heat conduction, convection and radiation. Once done, you have access to a temperature field across the sample (and the reactor).
We can now move to solving gas mass transfer equations, featuring diffusion, viscous flow and, of course, chemical deposition reactions. This process gives access to the repartition of chemical reactants and products throughout the material under processing and the reaction rates. Finally, you just have to use the resulting reaction rates to solve the solid mass balance equation, which yields the evolution of the characteristics of the materials after some infiltration time.
As showcased in the central part of the image that is the cover of this article, which is an example of what I elaborate in my laboratory, in the multi-physics modelling of CVI with Radio-Frequency heating, we can see the mesh production as well as the electromagnetic and heat transfer computation. On the right of the same image, we can see the simulation of the infiltration and its evolution in time.
Now we have to go back to the very beginning! Indeed, many materials characteristics have changed: the (complex) dielectric constant, the heat conductivity and capacity, the porosity, the density, the diffusion coefficients of the gases, and, last but not least, the internal surface area available for the chemical deposition reaction. As the late Prof. Stratis V. Sotirchos, a specialist of CVI modelling used to say: “This is a real-life dirty problem, that is, a problem in which everything depends on everything”.
Once we have had a look at the complex interplay of physicochemical phenomena, we still have a big unanswered question: how do the material properties depend on the degree of infiltration? We can answer such a question by considering the (hopefully) separate physical and chemical phenomena at a lower scale, i.e. inside the details of the porous medium.
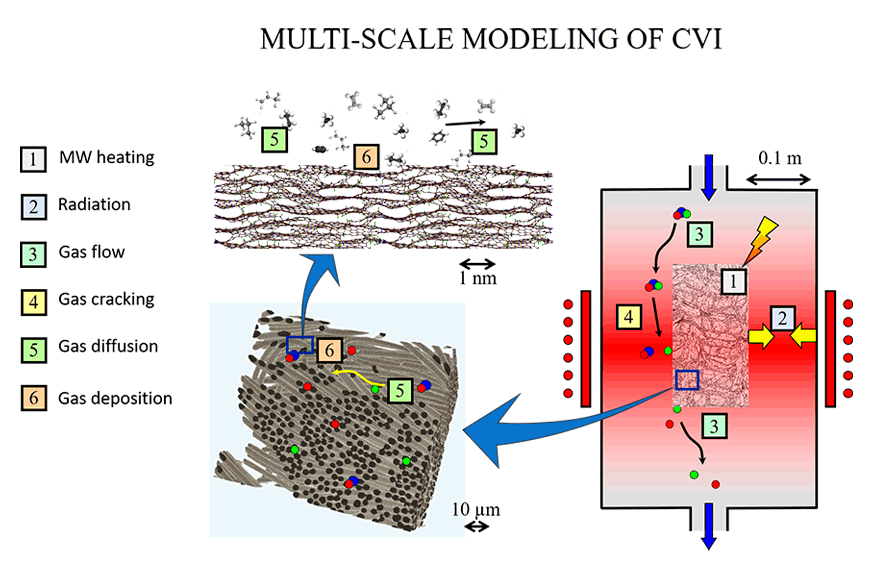
A solid method is to achieve image-based modelling. Computerized tomography or simple micrographs of the fibrous arrangement have proved to be sound bases to evaluate these properties. Image analysis techniques are helpful to correctly distinguish where the fibres, the growing matrix and the pores are in the material.
The next step is to produce numerical resolution domains for a computer to elaborate them with the equations’ solvers of the appropriate physics.
The final step consists of extracting average properties related to average quantities from the detailed results, for instance, an average conductivity that relates an average heat flux to an average temperature drop. Of course, the procedure should be repeated for different levels of infiltration.
Luckily, it is possible to perform numerical infiltrations rather than acquiring CT scans of the material at various infiltration stages. If the material displays two different length scales (i.e. a woven fabric), then this whole procedure should be performed at both. This brief explanation gives us an idea of the large number of calculations required to reach the desired objective.
For example, in work package five CEM-WAVE develops image-based numerical modelling methodologies using X-ray CMT and SEM micrographs data. Such modelling techniques use AI-aided tools starting from material properties (internal geometry, heat and mass transfer properties and complex dielectric permittivity into the operative ranges of interest), to determine optimal conditions for infiltration time, material quality and energy consumption.
Hopefully, Artificial Intelligence will increasingly help in this task going forward, as it is already doing in CEM-WAVE. First, in image analysis for automated pattern recognition, as is already detailed in the literature, but also in relating properties to structural evolution in a condensed fashion, for example, in creating “surrogate models”.
If you are interested in digging deeper into this topic, we suggest a couple of book chapters on the subject:
Gerard L. Vignoles, “Modeling of Chemical Vapor Infiltration Processes”, Chapter 17 of “Advances in Composites Manufacturing and Process Design “, P. Boisse Ed., Elsevier Woodhead Scientific. ISBN-13: 978-1-78242-307-2, Date de Publication: Juillet 2015. Pages : 415-458. (2016)
Francis Langlais and Gerard L. Vignoles, Chemical Vapor Infiltration Processing of Ceramic Matrix Composites. In: Peter W.R. Beaumont and Carl H. Zweben (editors-in-chief), Comprehensive Composite Materials II, 2nd Edition, ISBN-13: 978-0-08-100534-7, Vol. 5 (Marina B. Ruggles-Wrenn, volume editor), Chap. 5.4, pp. 86-129 (2018), part of Reference Module in Materials Science and Materials Engineering (Saleem Hashmi, editor-in-chief), Oxford: Elsevier, ISBN-13: 978-0-12-803581-8, pp. 1-44. (2017)
Enjoy your reading and continue to follow our blog for more exciting news on CEM-WAVE’s progress!