Thermo-structural ceramic composites for a better future
How do we get Ceramic Matrix Composite (CMC) materials beyond the aeronautical and aerospace sector?
Dr Federica Burgio and Dr Giuseppe Magnani (ENEA)
From an ecological and economic standpoint, the need for energy efficiency improvements is becoming urgent in all industry sectors. In particular, in the aeronautical and aerospace sectors, the main issue that guides the technological innovation is the requirement of lightweight materials able to withstand temperatures up to 1500°C and exhibit high mechanical properties, such as increased strength and wear resistance. The resistance to high temperatures and improved mechanical properties are essential to enhance the thermal efficiency, prolong the operating lifetime of the material’s components and reduce polluting carbon emissions.
Among the so-called thermo-structural ceramic composites, we find the non-oxide ceramic composites, based on carbon () and silicon carbide () and reinforced with long fibres. These materials sum up all the required high-performance characteristics, overcoming the drawbacks of traditionally used materials, such as metal and monolithic ceramics. Amidst the production techniques for ceramic composites, the Chemical Vapour Infiltration (CVI) is the most promising one. This process is highly flexible as it allows the production of different types of matrix materials and is the most suitable to set up complex structures.
Despite the first studies about the CVI process dating back to the 1960s and the significant progress made in understanding the complicated chemical and physical phenomena governing the process, we have not entirely understood it, yet. The scaling-up to the industrial level and its efficiency from the energetic, economic and environmental point of view are still limited, particularly in Italy. To further advance the studies on the CVI process, in 2006 a pilot-sized CVI/CVD plant was set up at the ENEA Laboratory of Materials Technologies Faenza (TEMAF) (Figure 1).
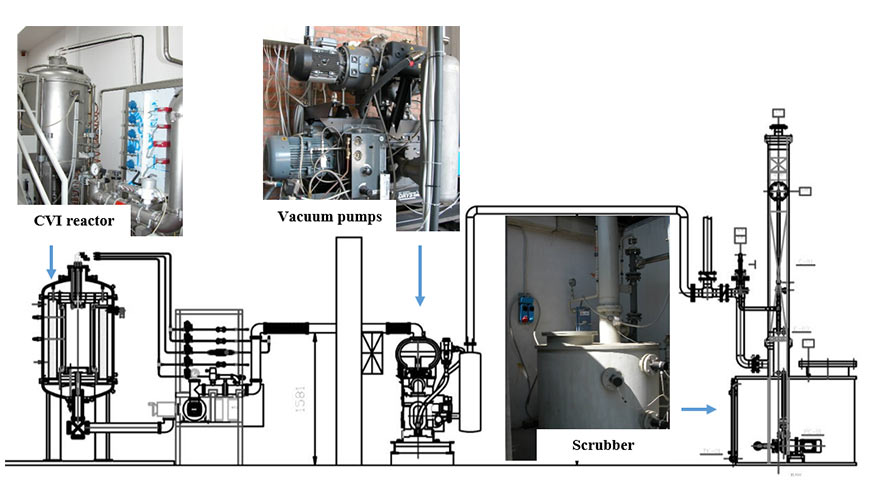
Figure 2: ENEA CVI plant. Source: ENEA
The related research activities performed at the plant mainly focus on the mechanisms of the CVI process and on evaluating the properties of the composite materials produced by the Lab. For instance, we studied the effect of the CVI process parameters, such as temperature and residence time, on Pyrolytic Carbon (Py-C) microstructure and the infiltration behaviour (fig. 2). Furthermore, the obtained experimental data, such as the deposition rates of Py-C and the density and porosity values of the produced Cf/C composites, were used to validate the calculation codes of the chemical vapour infiltration and deposition (CVI/CVD) processes.
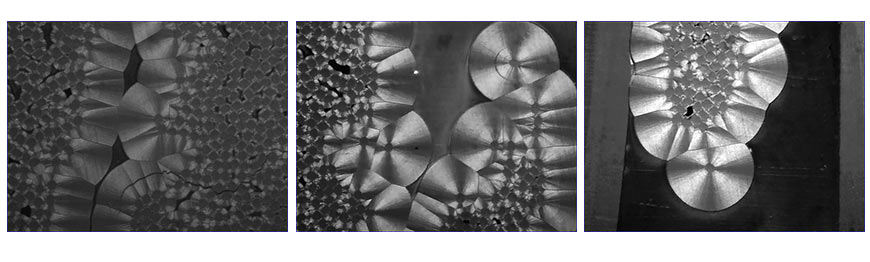
In addition, we conducted a preliminary study of silicon carbide Chemical Vapour Infiltration and Deposition (CVI/CVD) processes. The studies aimed at defining the CVI/CVD process parameters, starting from MethylTricoloroSilane (MTS) as SiC gaseous precursor (Figure 3).
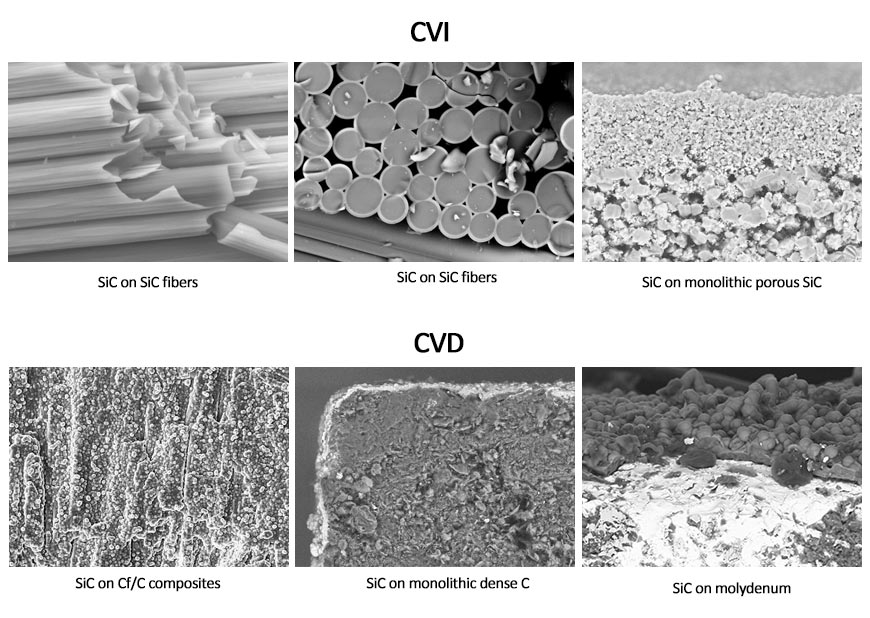
We carried out these research activities with funding from European and national institutions and within specific projects, as collaborations with companies, universities, and research centres. Due to their resistance properties, which make them able to withstand extreme environments, the non-oxide ceramic composite materials have been largely employed in the aeronautical and aerospace fields. For these reasons, ENEA's collaborations concentrated on developing components for aeronautical and aerospace applications, such as the leading and trailing edges of aircraft engine turbine blades. However, owing to their exceptional performances at high temperatures, the interest in using them for hard-to-abate industries, such as steel production, has been growing in recent years.
For example,CEM-WAVE(Novel Ceramic Matrix Composites produced with Microwave assisted Chemical Vapour Infiltration process for energy-intensive industries) is an ongoing project funded by the European Union’s Horizon 2020 research and innovation programme. To spearhead the shift to clean and renewable energies, the heavy industry needs best-performing and energy-efficient materials adapted to sustain harsh conditions, such as very high temperatures and corrosive environments. The CEM-WAVE project proposes to use Ceramic Matrix Composites in harsh-conditions manufacturing settings like steelmaking.
In 2020, the ENEA - Laboratory Materials Technologies Faenza joined the CEM-WAVE consortium believing that this application is an effective way to drive energy-intensive industrial sectors towards a suitable energy transition. Together with the other consortium members, we pursue the objective of furthering the understanding and the scientific research in ceramic composite development by CVI technology.
ENEA's activities within the project interlink with those of other project partners. The main interactions within the project are with the Department of Civil and Industrial Engineering of the University of Pisa (DICI-UNIPI), the Fraunhofer ISC - Center for High-Temperature Materials and Design, the School of Metallurgy and Materials of the University of Birmingham, and the GLANCE Group at the Instituto Politecnico di Torino (POLITO).
More specifically, ENEA leads the activities related to the work package 4 (WP4) of the CEM-WAVE project. In this WP, ENEA undertakes the physicochemical, microstructural, and mechanical characterisation of the CMCs to show that the newly developed materials perform better compared to currently used ones, particularly in terms of superior thermomechanical properties.
At the same time, we measure the thermomechanical, optical and thermophysical properties of the ox/ox, the SiCf/SiC, and their joints. In the case of SiCf/SiC, this happens only in the relevant passive oxidation temperature range. We also perform ageing tests in static and dynamic conditions (burner rigs). We carry out the described activities within WP4 in collaboration with CERTIMAC, ENEA’s linked third party. CERTIMAC provides its expertise in the thermophysical characterization, by assessing how the ceramic behaves in the developed solutions.
ENEA also contributes to the project by testing a pressure-less joining method for non-oxide CMCs based using a high-temperature resistant brazing mixture.
Are you interested in knowing more about thermo-structural ceramic composites and the CEM-WAVE project? Read more on the article ENEA-TEMAF recently published in "Compositi Magazine.